प्लाईवुड लकड़ी की तीन या उससे ज़्यादा पतली परतों से बना होता है, जिन्हें एक चिपकने वाले पदार्थ से जोड़ा जाता है। लकड़ी की हर परत या प्लाई को आमतौर पर इस तरह से बनाया जाता है कि उसका दाना बगल की परत के समकोण पर हो ताकि सिकुड़न को कम किया जा सके और तैयार टुकड़े की मज़बूती को बेहतर बनाया जा सके। ज़्यादातर प्लाईवुड को बड़ी, सपाट चादरों में दबाया जाता है, जिनका इस्तेमाल इमारत निर्माण में किया जाता है। अन्य प्लाईवुड के टुकड़ों को फर्नीचर, नावों और विमानों में इस्तेमाल के लिए सरल या मिश्रित वक्रों में बनाया जा सकता है।
निर्माण के साधन के रूप में लकड़ी की पतली परतों का उपयोग लगभग 1500 ईसा पूर्व से होता है जब मिस्र के कारीगरों ने राजा तुत-अंख-अमोन की कब्र में पाए गए देवदार के ताबूत के बाहरी हिस्से में गहरे आबनूस की लकड़ी के पतले टुकड़ों को जोड़ा था। इस तकनीक का इस्तेमाल बाद में यूनानियों और रोमनों ने बढ़िया फर्नीचर और अन्य सजावटी वस्तुओं के निर्माण के लिए किया। 1600 के दशक में, लकड़ी के पतले टुकड़ों से फर्नीचर को सजाने की कला को विनियरिंग के रूप में जाना जाने लगा, और टुकड़ों को खुद विनियर के रूप में जाना जाने लगा।
1700 के दशक के अंत तक, विनियर के टुकड़े पूरी तरह से हाथ से काटे जाते थे। 1797 में, अंग्रेज सर सैमुअल बेंथम ने विनियर बनाने के लिए कई मशीनों को कवर करने वाले पेटेंट के लिए आवेदन किया। अपने पेटेंट आवेदनों में, उन्होंने गोंद के साथ विनियर की कई परतों को लेमिनेट करके एक मोटा टुकड़ा बनाने की अवधारणा का वर्णन किया - जिसे हम अब प्लाईवुड कहते हैं, उसका पहला विवरण।
इस विकास के बावजूद, फर्नीचर उद्योग के बाहर लैमिनेटेड विनियर को कोई व्यावसायिक उपयोग मिलने में लगभग सौ साल लग गए। लगभग 1890 में, लैमिनेटेड लकड़ी का इस्तेमाल पहली बार दरवाज़े बनाने के लिए किया गया था। जैसे-जैसे मांग बढ़ी, कई कंपनियों ने न केवल दरवाज़ों के लिए, बल्कि रेलरोड कारों, बसों और हवाई जहाजों में इस्तेमाल के लिए भी मल्टीपल-प्लाई लैमिनेटेड लकड़ी की चादरें बनाना शुरू कर दिया। इस बढ़ते उपयोग के बावजूद, "चिपकाई गई लकड़ी" का उपयोग करने की अवधारणा, जैसा कि कुछ कारीगर व्यंग्यात्मक रूप से उन्हें कहते हैं, ने उत्पाद के लिए एक नकारात्मक छवि उत्पन्न की। इस छवि का मुकाबला करने के लिए, लैमिनेटेड लकड़ी के निर्माताओं ने बैठक की और अंततः नई सामग्री का वर्णन करने के लिए "प्लाईवुड" शब्द पर सहमति व्यक्त की।
1928 में, संयुक्त राज्य अमेरिका में सामान्य निर्माण सामग्री के रूप में उपयोग के लिए पहली मानक आकार की 4 फीट गुणा 8 फीट (1.2 मीटर गुणा 2.4 मीटर) प्लाईवुड शीट पेश की गई थी। अगले दशकों में, बेहतर चिपकने वाले पदार्थों और उत्पादन के नए तरीकों ने प्लाईवुड को कई तरह के अनुप्रयोगों के लिए इस्तेमाल करने की अनुमति दी। आज, प्लाईवुड ने कई निर्माण उद्देश्यों के लिए कटी हुई लकड़ी की जगह ले ली है, और प्लाईवुड निर्माण एक बहु-बिलियन डॉलर, विश्वव्यापी उद्योग बन गया है।
प्लाईवुड की बाहरी परतों को क्रमशः फेस और बैक के नाम से जाना जाता है। फेस वह सतह है जिसका उपयोग किया जाना है या जिसे देखा जाना है, जबकि बैक अप्रयुक्त या छिपा रहता है। केंद्र परत को कोर के नाम से जाना जाता है। पांच या उससे अधिक परतों वाले प्लाईवुड में, मध्यवर्ती परतों को क्रॉसबैंड के नाम से जाना जाता है।
प्लाईवुड को हार्डवुड, सॉफ्टवुड या दोनों के संयोजन से बनाया जा सकता है। कुछ सामान्य हार्डवुड में ऐश, मेपल, महोगनी, ओक और सागौन शामिल हैं। संयुक्त राज्य अमेरिका में प्लाईवुड बनाने के लिए इस्तेमाल की जाने वाली सबसे आम सॉफ्टवुड डगलस फ़िर है, हालांकि पाइन, देवदार, स्प्रूस और रेडवुड की कई किस्मों का भी उपयोग किया जाता है।
कम्पोजिट प्लाईवुड में पार्टिकलबोर्ड या ठोस लकड़ी के टुकड़ों से बना कोर होता है जो किनारे से किनारे तक जुड़ा होता है। इसे प्लाईवुड के सामने और पीछे से फिनिश किया जाता है। कम्पोजिट प्लाईवुड का उपयोग वहां किया जाता है जहां बहुत मोटी शीट की आवश्यकता होती है।
लकड़ी की परतों को आपस में जोड़ने के लिए इस्तेमाल किए जाने वाले चिपकने वाले पदार्थ का प्रकार तैयार प्लाईवुड के लिए विशिष्ट अनुप्रयोग पर निर्भर करता है। संरचना के बाहरी भाग पर स्थापना के लिए डिज़ाइन की गई सॉफ्टवुड प्लाईवुड शीट में आमतौर पर एक चिपकने वाले पदार्थ के रूप में फिनोल-फॉर्मेल्डिहाइड राल का उपयोग किया जाता है क्योंकि इसकी उत्कृष्ट शक्ति और नमी के प्रति प्रतिरोध होता है। संरचना के अंदरूनी भाग पर स्थापना के लिए डिज़ाइन की गई सॉफ्टवुड प्लाईवुड शीट में रक्त प्रोटीन या सोयाबीन प्रोटीन चिपकने वाला पदार्थ इस्तेमाल किया जा सकता है, हालाँकि अधिकांश सॉफ्टवुड आंतरिक शीट अब बाहरी शीट के लिए इस्तेमाल किए जाने वाले समान फिनोल-फॉर्मेल्डिहाइड राल से बनाई जाती हैं। आंतरिक अनुप्रयोगों और फर्नीचर के निर्माण में उपयोग किए जाने वाले हार्डवुड प्लाईवुड को आमतौर पर यूरिया-फॉर्मेल्डिहाइड राल से बनाया जाता है।
कुछ अनुप्रयोगों के लिए प्लाईवुड शीट की आवश्यकता होती है जिसमें प्लास्टिक, धातु, या राल-संसेचित कागज या कपड़े की एक पतली परत होती है जो या तो सामने या पीछे (या दोनों) से जुड़ी होती है ताकि बाहरी सतह को नमी और घर्षण के लिए अतिरिक्त प्रतिरोध दिया जा सके या इसके पेंट-होल्डिंग गुणों को बेहतर बनाया जा सके। इस तरह के प्लाईवुड को ओवरलेड प्लाईवुड कहा जाता है और इसका उपयोग आमतौर पर निर्माण, परिवहन और कृषि उद्योगों में किया जाता है।
अन्य प्लाईवुड शीटों को सतहों को परिष्कृत रूप देने के लिए तरल दाग के साथ लेपित किया जा सकता है, या प्लाईवुड के अग्नि प्रतिरोध या क्षय के प्रतिरोध को बेहतर बनाने के लिए विभिन्न रसायनों के साथ उपचार किया जा सकता है।
प्लाईवुड की दो व्यापक श्रेणियां हैं, जिनमें से प्रत्येक की अपनी ग्रेडिंग प्रणाली है।
एक वर्ग को निर्माण और औद्योगिक के रूप में जाना जाता है। इस वर्ग के प्लाईवुड का उपयोग मुख्य रूप से उनकी मजबूती के लिए किया जाता है और उनकी एक्सपोज़र क्षमता और चेहरे और पीछे इस्तेमाल किए गए विनियर के ग्रेड के आधार पर मूल्यांकन किया जाता है। एक्सपोज़र क्षमता आंतरिक या बाहरी हो सकती है, जो गोंद के प्रकार पर निर्भर करती है। विनियर ग्रेड N, A, B, C या D हो सकते हैं। N ग्रेड में बहुत कम सतही दोष होते हैं, जबकि D ग्रेड में कई गांठें और दरारें हो सकती हैं। उदाहरण के लिए, किसी घर में सबफ़्लोरिंग के लिए इस्तेमाल किए जाने वाले प्लाईवुड को "इंटीरियर CD" रेट किया जाता है। इसका मतलब है कि इसमें C फेस और D बैक है, और गोंद सुरक्षित स्थानों में उपयोग के लिए उपयुक्त है। सभी निर्माण और औद्योगिक प्लाईवुड की आंतरिक परतें ग्रेड C या D विनियर से बनी होती हैं, चाहे रेटिंग कुछ भी हो।
प्लाईवुड के दूसरे वर्ग को हार्डवुड और डेकोरेटिव के रूप में जाना जाता है। इस वर्ग के प्लाईवुड का उपयोग मुख्य रूप से उनकी दिखावट के लिए किया जाता है और उन्हें नमी के प्रतिरोध के अवरोही क्रम में तकनीकी (बाहरी), प्रकार I (बाहरी), प्रकार II (आंतरिक) और प्रकार III (आंतरिक) के रूप में वर्गीकृत किया जाता है। उनके फेस विनियर वस्तुतः दोषों से मुक्त होते हैं।
आकार
प्लाईवुड शीट की मोटाई 0.06 इंच (1.6 मिमी) से लेकर 3.0 इंच (76 मिमी) तक होती है। सबसे आम मोटाई 0.25 इंच (6.4 मिमी) से लेकर 0.75 इंच (19.0 मिमी) तक होती है। हालाँकि प्लाईवुड की शीट का कोर, क्रॉसबैंड और चेहरा और पिछला हिस्सा अलग-अलग मोटाई के लिबास से बना हो सकता है, लेकिन प्रत्येक की मोटाई केंद्र के चारों ओर संतुलित होनी चाहिए। उदाहरण के लिए, चेहरा और पिछला हिस्सा बराबर मोटाई का होना चाहिए। इसी तरह ऊपर और नीचे के क्रॉसबैंड भी बराबर होने चाहिए।
भवन निर्माण में इस्तेमाल की जाने वाली प्लाईवुड शीट का सबसे आम आकार 4 फीट (1.2 मीटर) चौड़ा और 8 फीट (2.4 मीटर) लंबा होता है। अन्य सामान्य चौड़ाई 3 फीट (0.9 मीटर) और 5 फीट (1.5 मीटर) हैं। लंबाई 1 फीट (0.3 मीटर) की वृद्धि में 8 फीट (2.4 मीटर) से 12 फीट (3.6 मीटर) तक भिन्न होती है। नाव निर्माण जैसे विशेष अनुप्रयोगों के लिए बड़ी शीट की आवश्यकता हो सकती है।
प्लाईवुड बनाने के लिए इस्तेमाल किए जाने वाले पेड़ आम तौर पर लकड़ी बनाने के लिए इस्तेमाल किए जाने वाले पेड़ों की तुलना में व्यास में छोटे होते हैं। ज़्यादातर मामलों में, उन्हें प्लाईवुड कंपनी के स्वामित्व वाले क्षेत्रों में लगाया और उगाया गया है। इन क्षेत्रों को पेड़ों की वृद्धि को अधिकतम करने और कीड़ों या आग से होने वाले नुकसान को कम करने के लिए सावधानीपूर्वक प्रबंधित किया जाता है।
यहां पेड़ों को मानक 4 फीट गुणा 8 फीट (1.2 मीटर गुणा 2.4 मीटर) प्लाईवुड शीट में बदलने के लिए कार्यों का एक विशिष्ट क्रम दिया गया है:
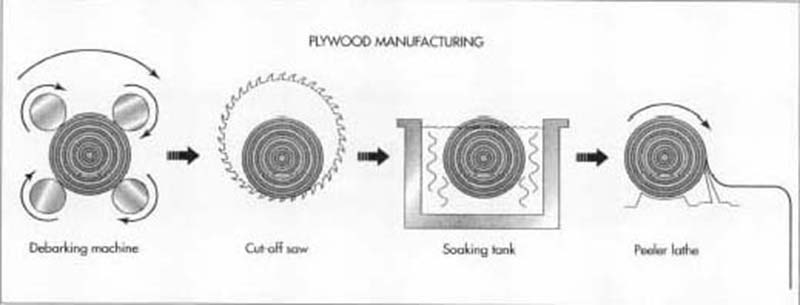
सबसे पहले लकड़ियों की छाल उतारी जाती है और फिर उन्हें छीलने वाले ब्लॉकों में काटा जाता है। ब्लॉकों को लिबास की पट्टियों में काटने के लिए, उन्हें पहले भिगोया जाता है और फिर छीलकर पट्टियाँ बनाई जाती हैं।
1 किसी क्षेत्र में चयनित पेड़ों को काटने या गिराने के लिए तैयार के रूप में चिह्नित किया जाता है। कटाई गैसोलीन से चलने वाली चेन आरी या फ़ेलर नामक पहिएदार वाहनों के सामने लगे बड़े हाइड्रोलिक कैंची से की जा सकती है। गिरे हुए पेड़ों से शाखाओं को चेन आरी से हटाया जाता है।
2 कटे हुए पेड़ के तने या लट्ठों को स्किडर नामक पहिएदार वाहनों द्वारा लोडिंग क्षेत्र में खींचा जाता है। लट्ठों को लंबाई में काटा जाता है और प्लाईवुड मिल की यात्रा के लिए ट्रकों पर लादा जाता है, जहाँ उन्हें लॉग डेक के रूप में जाने जाने वाले लंबे ढेर में रखा जाता है।
3 जैसे-जैसे लकड़ियों की ज़रूरत होती है, उन्हें रबर टायर वाले लोडर द्वारा लॉग डेक से उठाया जाता है और चेन कन्वेयर पर रखा जाता है जो उन्हें डीबार्किंग मशीन तक ले जाता है। यह मशीन छाल को हटाती है, या तो तीखे दाँतों वाले पीसने वाले पहियों से या उच्च दबाव वाले पानी के जेट से, जबकि लॉग को धीरे-धीरे अपनी लंबी धुरी पर घुमाया जाता है।
4 छाल उतारे गए लॉग को चेन कन्वेयर पर मिल में ले जाया जाता है, जहाँ एक विशाल गोलाकार आरी उन्हें लगभग 8 फीट-4 इंच (2.5 मीटर) से 8 फीट-6 इंच (2.6 मीटर) लंबे खंडों में काटती है, जो मानक 8 फीट (2.4 मीटर) लंबी शीट बनाने के लिए उपयुक्त होते हैं। इन लॉग खंडों को पीलर ब्लॉक के रूप में जाना जाता है।
5 विनियर को काटने से पहले, लकड़ी को नरम करने के लिए पीलर ब्लॉक को गर्म करके भिगोना चाहिए। ब्लॉक को भाप में पकाया जा सकता है या गर्म पानी में डुबोया जा सकता है। लकड़ी के प्रकार, ब्लॉक के व्यास और अन्य कारकों के आधार पर इस प्रक्रिया में 12-40 घंटे लगते हैं।
6 गर्म किए गए पीलर ब्लॉक को फिर पीलर खराद में ले जाया जाता है, जहाँ वे स्वचालित रूप से संरेखित होते हैं और एक-एक करके खराद में डाले जाते हैं। जैसे ही खराद ब्लॉक को अपनी लंबी धुरी पर तेज़ी से घुमाता है, एक पूरी लंबाई वाला चाकू ब्लेड 300-800 फीट/मिनट (90-240 मीटर/मिनट) की दर से घूमते हुए ब्लॉक की सतह से लिबास की एक सतत शीट छीलता है। जब ब्लॉक का व्यास लगभग 3-4 इंच (230-305 मिमी) तक कम हो जाता है, तो लकड़ी का बचा हुआ टुकड़ा, जिसे पीलर कोर के रूप में जाना जाता है, खराद से बाहर निकाल दिया जाता है और एक नया पीलर ब्लॉक उसकी जगह पर डाला जाता है।
7 पीलर लेथ से निकलने वाली विनियर की लंबी शीट को तुरंत संसाधित किया जा सकता है, या इसे लंबी, बहु-स्तरीय ट्रे में संग्रहीत किया जा सकता है या रोल पर लपेटा जा सकता है। किसी भी मामले में, अगली प्रक्रिया में विनियर को उपयोग करने योग्य चौड़ाई में काटना शामिल है, आमतौर पर लगभग 4 फीट-6 इंच (1.4 मीटर), मानक 4 फीट (1.2 मीटर) चौड़ी प्लाईवुड शीट बनाने के लिए। उसी समय, ऑप्टिकल स्कैनर अस्वीकार्य दोषों वाले खंडों की तलाश करते हैं, और इन्हें काट दिया जाता है, जिससे विनियर के मानक चौड़ाई से कम टुकड़े रह जाते हैं।
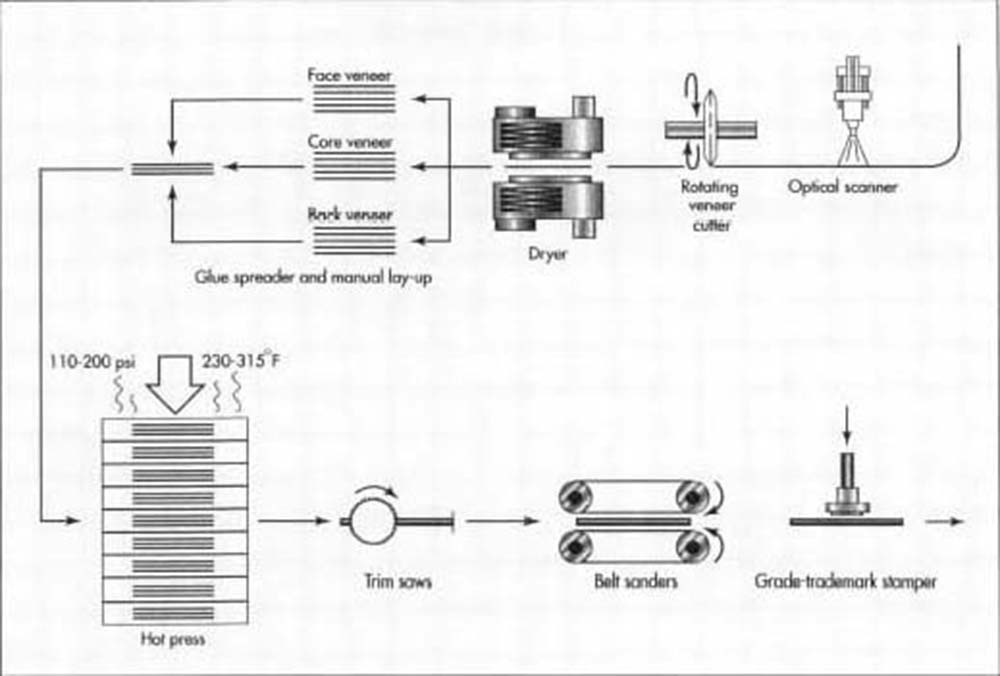
विनियर की गीली पट्टियों को रोल में लपेटा जाता है, जबकि ऑप्टिकल स्कैनर लकड़ी में किसी भी अस्वीकार्य दोष का पता लगाता है। एक बार सूख जाने पर विनियर को ग्रेड किया जाता है और स्टैक किया जाता है। विनियर के चयनित खंडों को एक साथ चिपकाया जाता है। विनियर को प्लाईवुड के एक ठोस टुकड़े में सील करने के लिए एक गर्म प्रेस का उपयोग किया जाता है, जिसे उसके उचित ग्रेड के साथ मुहर लगाने से पहले ट्रिम और सैंड किया जाएगा।
8 फिर विनियर के खंडों को ग्रेड के अनुसार छांटा और स्टैक किया जाता है। यह मैन्युअल रूप से किया जा सकता है, या ऑप्टिकल स्कैनर का उपयोग करके स्वचालित रूप से किया जा सकता है।
9 छांटे गए टुकड़ों को एक ड्रायर में डाला जाता है ताकि उनकी नमी कम हो जाए और उन्हें एक साथ चिपकाए जाने से पहले सिकुड़ने दिया जा सके। अधिकांश प्लाईवुड मिलें एक यांत्रिक ड्रायर का उपयोग करती हैं जिसमें टुकड़े एक गर्म कक्ष के माध्यम से लगातार चलते रहते हैं। कुछ ड्रायर में, सुखाने की प्रक्रिया को तेज करने के लिए टुकड़ों की सतह पर उच्च-वेग, गर्म हवा के जेट उड़ाए जाते हैं।
10 जैसे ही विनियर के हिस्से ड्रायर से बाहर निकलते हैं, उन्हें ग्रेड के अनुसार स्टैक किया जाता है। अंडरविड्थ सेक्शन में अतिरिक्त विनियर को टेप या गोंद के साथ जोड़ा जाता है ताकि टुकड़ों को आंतरिक परतों में उपयोग के लिए उपयुक्त बनाया जा सके जहाँ दिखावट और मजबूती कम महत्वपूर्ण होती है।
11 विनियर के वे भाग जिन्हें क्रॉसवाइज स्थापित किया जाएगा - तीन-परत शीट में कोर, या पांच-परत शीट में क्रॉसबैंड - लगभग 4 फीट-3 इंच (1.3 मीटर) की लंबाई में काटा जाता है।
12 जब प्लाईवुड के किसी विशेष भाग के लिए विनियर के उपयुक्त भाग इकट्ठे हो जाते हैं, तो टुकड़ों को बिछाने और एक साथ चिपकाने की प्रक्रिया शुरू होती है। यह मैन्युअल रूप से या मशीनों के साथ अर्ध-स्वचालित रूप से किया जा सकता है। तीन-परत शीट के सबसे सरल मामले में, पीछे के विनियर को सपाट रखा जाता है और एक गोंद फैलाने वाले उपकरण के माध्यम से चलाया जाता है, जो ऊपरी सतह पर गोंद की एक परत लगाता है। कोर विनियर के छोटे खंडों को फिर चिपके हुए पीछे के शीर्ष पर क्रॉसवेज रखा जाता है, और पूरी शीट को दूसरी बार गोंद फैलाने वाले उपकरण के माध्यम से चलाया जाता है। अंत में, फेस विनियर को चिपके हुए कोर के ऊपर रखा जाता है, और शीट को प्रेस में जाने के लिए प्रतीक्षा कर रही अन्य शीट के साथ स्टैक किया जाता है।
13 चिपकी हुई चादरें एक बहु-खुले गर्म प्रेस में लोड की जाती हैं। प्रेस एक बार में 20-40 शीट संभाल सकती हैं, जिसमें प्रत्येक शीट एक अलग स्लॉट में लोड की जाती है। जब सभी शीट लोड हो जाती हैं, तो प्रेस उन्हें लगभग 110-200 psi (7.6-13.8 बार) के दबाव में एक साथ दबाता है, जबकि उसी समय उन्हें लगभग 230-315° F (109.9-157.2° C) के तापमान पर गर्म करता है। दबाव विनियर की परतों के बीच अच्छे संपर्क को सुनिश्चित करता है, और गर्मी गोंद को अधिकतम मजबूती के लिए ठीक से ठीक करने का कारण बनती है। 2-7 मिनट की अवधि के बाद, प्रेस को खोला जाता है और शीट को उतार दिया जाता है।
14 फिर रफ शीट को आरी के एक सेट से गुजारा जाता है, जो उन्हें उनकी अंतिम चौड़ाई और लंबाई तक ट्रिम करता है। उच्च ग्रेड शीट 4 फीट (1.2 मीटर) चौड़े बेल्ट सैंडर्स के एक सेट से गुजरती हैं, जो सामने और पीछे दोनों तरफ सैंड करते हैं। इंटरमीडिएट ग्रेड शीट को खुरदरे क्षेत्रों को साफ करने के लिए मैन्युअल रूप से स्पॉट सैंड किया जाता है। कुछ शीट को गोलाकार आरी ब्लेड के एक सेट से गुजारा जाता है, जो प्लाईवुड को एक बनावट वाला रूप देने के लिए सामने की तरफ उथले खांचे काटते हैं। अंतिम निरीक्षण के बाद, किसी भी शेष दोष की मरम्मत की जाती है।
15 तैयार शीट पर ग्रेड-ट्रेडमार्क की मुहर लगाई जाती है जो खरीदार को एक्सपोजर रेटिंग, ग्रेड, मिल नंबर और अन्य कारकों के बारे में जानकारी देता है। एक ही ग्रेड-ट्रेडमार्क की शीट को एक साथ स्टैक में बांधा जाता है और शिपमेंट की प्रतीक्षा के लिए गोदाम में ले जाया जाता है।
लकड़ी की तरह ही, प्लाईवुड का कोई भी टुकड़ा परफेक्ट नहीं होता। प्लाईवुड के सभी टुकड़ों में कुछ हद तक दोष होते हैं। इन दोषों की संख्या और स्थान प्लाईवुड ग्रेड निर्धारित करते हैं। निर्माण और औद्योगिक प्लाईवुड के लिए मानक राष्ट्रीय मानक ब्यूरो और अमेरिकी प्लाईवुड एसोसिएशन द्वारा तैयार उत्पाद मानक PS1 द्वारा परिभाषित किए जाते हैं। हार्डवुड और सजावटी प्लाईवुड के लिए मानक अमेरिकी राष्ट्रीय मानक संस्थान और हार्डवुड प्लाईवुड मैन्युफैक्चरर्स एसोसिएशन द्वारा तैयार ANSIIHPMA HP द्वारा परिभाषित किए जाते हैं। ये मानक न केवल प्लाईवुड के लिए ग्रेडिंग सिस्टम स्थापित करते हैं, बल्कि निर्माण, प्रदर्शन और अनुप्रयोग मानदंड भी निर्दिष्ट करते हैं।
हालाँकि प्लाईवुड पेड़ों का काफी कुशल उपयोग करता है - मूल रूप से उन्हें अलग करना और उन्हें एक मजबूत, अधिक उपयोगी विन्यास में वापस जोड़ना - फिर भी विनिर्माण प्रक्रिया में काफी अपशिष्ट निहित है। ज्यादातर मामलों में, पेड़ में लकड़ी की उपयोगी मात्रा का केवल 50-75% ही प्लाईवुड में परिवर्तित किया जाता है। इस आंकड़े को बेहतर बनाने के लिए, कई नए उत्पाद विकसित किए जा रहे हैं।
एक नए उत्पाद को ओरिएंटेड स्ट्रैंड बोर्ड कहा जाता है, जो लॉग से एक लिबास को छीलने और कोर को त्यागने के बजाय पूरे लॉग को स्ट्रैंड में काटकर बनाया जाता है। स्ट्रैंड को एक चिपकने वाले पदार्थ के साथ मिलाया जाता है और एक दिशा में अनाज चलाने के साथ परतों में संपीड़ित किया जाता है। इन संपीड़ित परतों को फिर एक दूसरे के समकोण पर प्लाईवुड की तरह उन्मुख किया जाता है, और एक साथ जोड़ा जाता है। ओरिएंटेड स्ट्रैंड बोर्ड प्लाईवुड जितना ही मजबूत होता है और इसकी कीमत थोड़ी कम होती है।
पोस्ट करने का समय: अगस्त-10-2021